What Is Silicone Rubber Compression Molding?
Silicone rubber component molding is a complex and specialized process, particularly when producing silicone products. Multiple molding techniques are available, each demanding careful evaluation by manufacturers. The choice of molding method is influenced by several critical factors, and among the various techniques, two of the most prominent are compression molding and liquid silicone injection molding (LIM).
In the production of silicone products, one common method involves labor-intensive silicone rubber molding, especially when using a pre-catalyzed silicone product mixed with pigment for added color. The pre-catalyzed silicone, combined with the pigment, enables easier curing when subjected to heat, which is essential for achieving the desired properties of the silicone products.
The labor-intensive aspect of this process comes into play during the pigment mixing stage. Technicians use a two-mill roll to achieve a thorough and consistent color distribution in the silicone products. However, this step carries a risk of introducing contamination to the silicone, which could affect the quality of the final silicone products.
Once the silicone is pre-catalyzed and pigmented, technicians weigh and shape it according to the required size and configuration for the specific silicone product. The prepared silicone is then placed in the mold cavity, where it undergoes compression between top and bottom plates.
The next step in creating silicone products involves heating the plates to melt and cure the silicone, completing the compression molding process. While compression molding is the simplest method for molding silicone products, it does entail significant manual labor, particularly during the preparation and handling of the silicone materials.
To manage manufacturing costs, fillers can be added to the silicone material, which helps reduce overall production expenses.
Silicone rubber compression molding offers numerous advantages, including the ability to produce complex shapes, precise dimensions, and high-quality surface finishes. This method is widely utilized for producing high-quality, durable parts with complex geometries and tight tolerances.
Silicone Rubber Compression Molding Process
Material Preparation: The process for creating silicone products begins with preparing a pre-measured amount of uncured silicone rubber. This silicone is typically in the form of a "preform" specifically shaped to fit the mold cavity. Additives such as curing agents, catalysts, fillers, colorants, and other performance-enhancing substances may be included to tailor the properties of the final silicone products.
Mold Setup: The prepared preform is placed into a preheated mold, which consists of two halves—an upper and a lower part. The mold is then closed to start the molding process for the silicone products.
Compression and Curing: The closed mold is subjected to pressure using a hydraulic press. The combination of heat and pressure causes the silicone rubber to flow and fill the mold cavity completely. This process also initiates the curing phase, where the silicone rubber hardens into the desired shape of the silicone products.
Demolding and Trimming: Once the silicone products have cooled down, they are carefully removed from the mold. During the demolding process, special attention is given to avoid damaging the silicone products. Any excess material, known as flash, is trimmed or removed to ensure the final products meet quality standards.
Benefits of Silicone Compression Molding
Competitive Cost
Fast Mold Making, Lower Cost
Suitable for Large Order Demand
Class 8 Cleaning Room
Silicone Compression Molding VS Liquid Injection Molding
Cost-effective: Compression molding is generally more cost-effective than liquid injection molding, largely due to its simpler mold design and the capability to produce multiple cavities without the need for expensive tooling.
Quick Mold Making: Compression molding boasts shorter mold making times, typically taking around 15-20 days, and for simpler parts, just 7-10 days are sufficient. In contrast, liquid injection molding requires a longer period of 40-55 days for mold fabrication.
Simplified Maintenance: Compression molds have a straightforward structure, making them easier to maintain and set up compared to liquid silicone injection molds. Setting up a silicone compression mold typically takes only about 1 hour, while assembly for a liquid silicone injection mold can take around 1 day.
Versatile Material Choices: Compression molding offers a wide range of material options, especially suitable for flexible materials that retain pliability after the curing process. Moreover, it accommodates thermosets, allowing the molding of multiple cavities. Commonly utilized materials include silicone, natural rubber, and EPDM.
Ample Production Capacity: Compression molding machines typically have high production capacity, allowing for efficient mass production. The ability to incorporate multiple cavities in a compression mold results in a higher output compared to injection molding methods.
Variety of Color Options: Compression molding offers greater flexibility for color testing compared to liquid injection molding. In compression molding, the mold can be easily cleaned, and different colored silicone can be milled and placed into the cavity for various color tests. In contrast, liquid injection molding requires a more time-intensive process, typically taking around half a day to clean the color system and needles, leading to significant time and material waste. Consequently, liquid injection molding is generally not preferred for testing different colors.
Application of Compression Molding Products
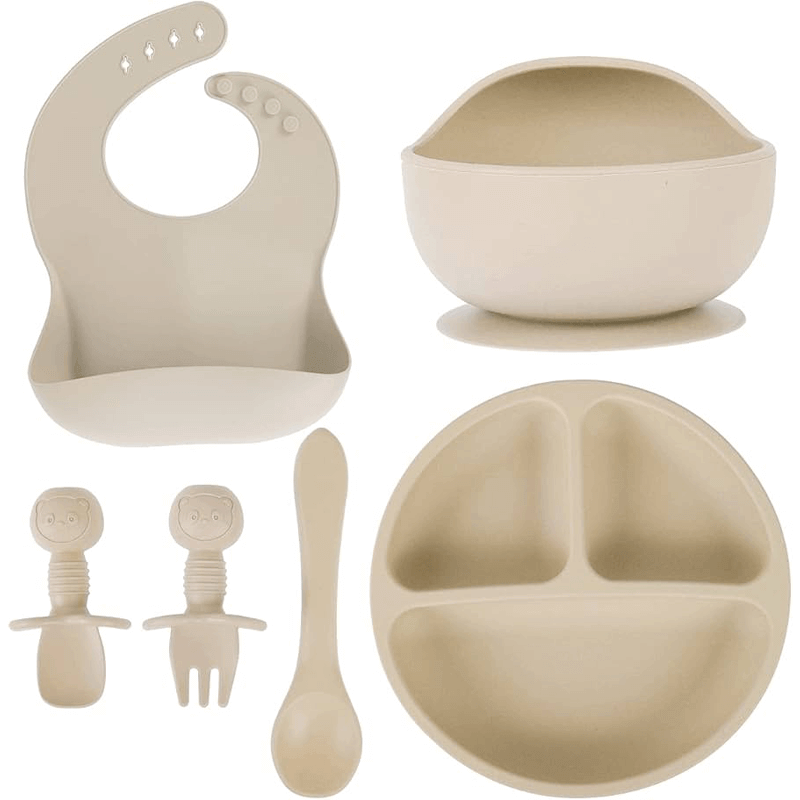

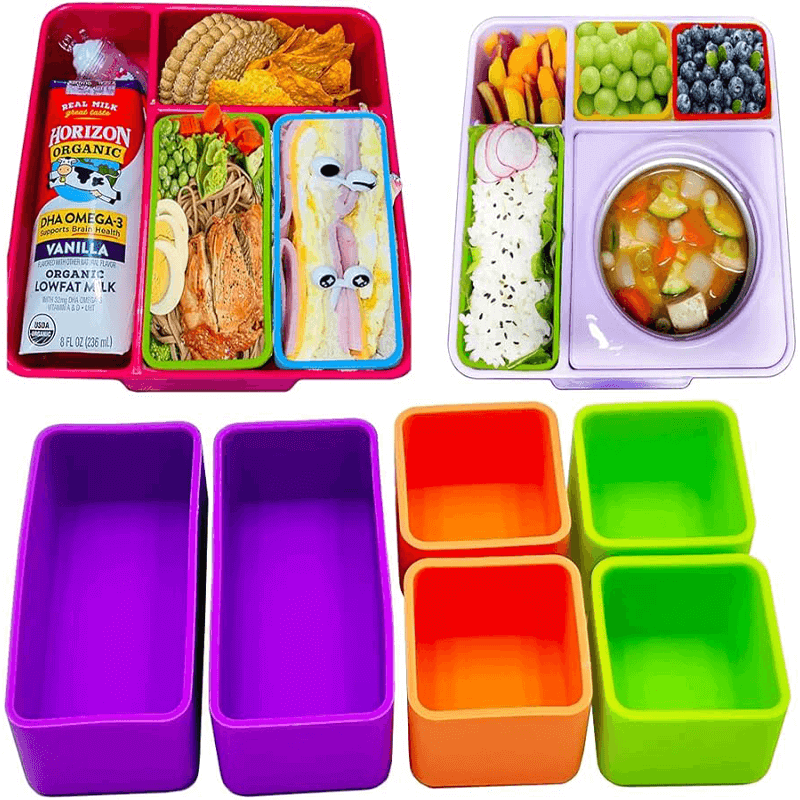
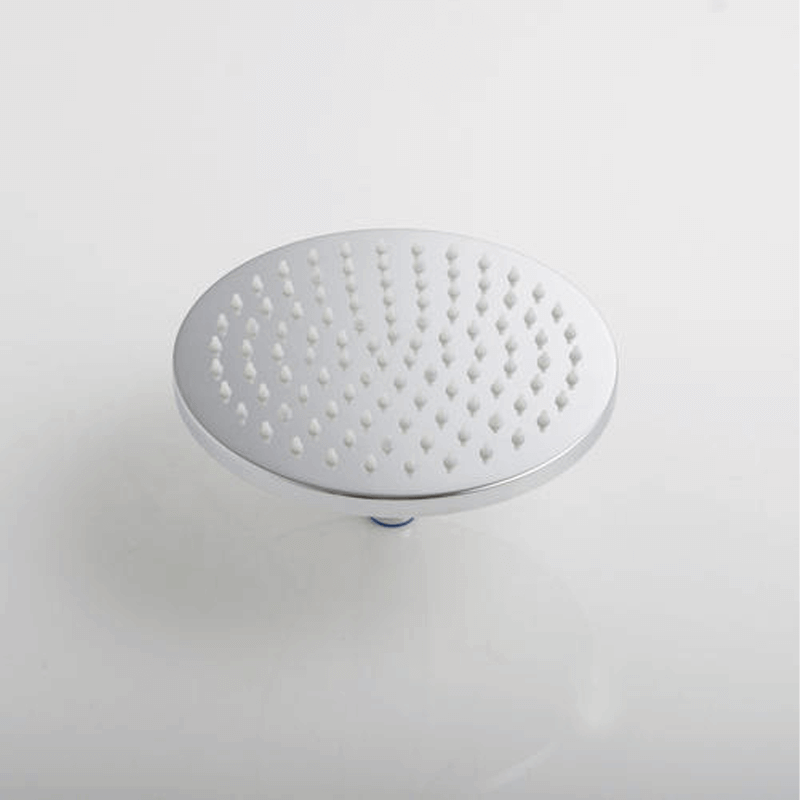