Precision Tooling & Versatile Mold Solutions
We are equipped to manufacture multiple molds simultaneously, thanks to our in-house team of experienced journeyman tool and die makers who leverage full CNC machining capabilities. Our efficient team specializes in creating cost-effective Reaction Injection Molding (RIM) tools, offering a range of price points and tool lifespans tailored to fit your project and budget requirements. By providing flexible tooling options, we ensure that our customers invest only as much as needed to meet their product's volume demands.
We excel in producing both small and large molds from machined aluminum. Whether you need fully customized aluminum molds with water lines and ejector systems or simpler molds without these features, we have the capability to meet your specific needs. Our RIM molding process is ideal for prototyping, short-term production, and other low-volume projects, providing a versatile and cost-effective solution for your silicone molding requirements.
Why Choose Us For Your Tooling Making
World-Class Craftsmanship
Our customers rely on us to build injection tools that many others shy away from. With our team of seasoned craftsmen, we bring a wealth of experience and industry expertise to create the complex tools required in today’s demanding market.
On-Time Delivery
We recognize that downtime directly impacts your profitability. That’s why we employ a state-of-the-art ERP system to meticulously track the progress of all projects. We’re committed to delivering on time, and we only take on projects if we’re confident we can meet your deadlines.
Fair Pricing
While offshoring might seem like a cost-saving option, it often fails to account for the true total cost of ownership, including the responsiveness to engineering changes and emergency repairs. Our transparent pricing reflects our commitment to providing value beyond just the initial tool cost.
Cutting-Edge Technology
Our advanced technological capabilities set us apart. We utilize precision 5-axis mills for creating intricate shapes, advanced CNC machines for handling large-scale projects, next-generation CAD/CAM software for optimized design, and high-speed machining to enhance efficiency and accuracy. This ensures that we deliver exceptional quality tools, tailored to meet your specific needs.
Seamless Prototyping for Efficient Tooling Making
At our company, we specialize in delivering rapid prototype parts that are critical in the tooling making process. By producing cast urethane prototypes in-house, we significantly reduce lead times, enabling the molding of both preliminary and final part designs. Prototypes are invaluable for various purposes, such as new project design verification, short production runs, bridge tooling, or as display parts for events like tradeshows.
Our prototyping process begins with Stereolithography (SLA) models, generated directly from CAD files, to create precise silicone molds. These molds allow us to produce cast urethane parts with exceptionally short lead times. These prototype molds can also function as bridge tooling, serving your needs until full-scale production molds are completed for Reaction Injection Molding (RIM).
The integration of both prototype and production RIM parts under one roof allows us to offer expert in-house engineering design guidance during your prototyping phase. This approach enables our customers to test parts in a production-like environment, eliminating the need for costly and time-consuming design for manufacture (DFM) adjustments post-prototyping. Ultimately, this streamlined process not only saves time and costs but also ensures that your tooling making is aligned with both prototype and production requirements from the outset
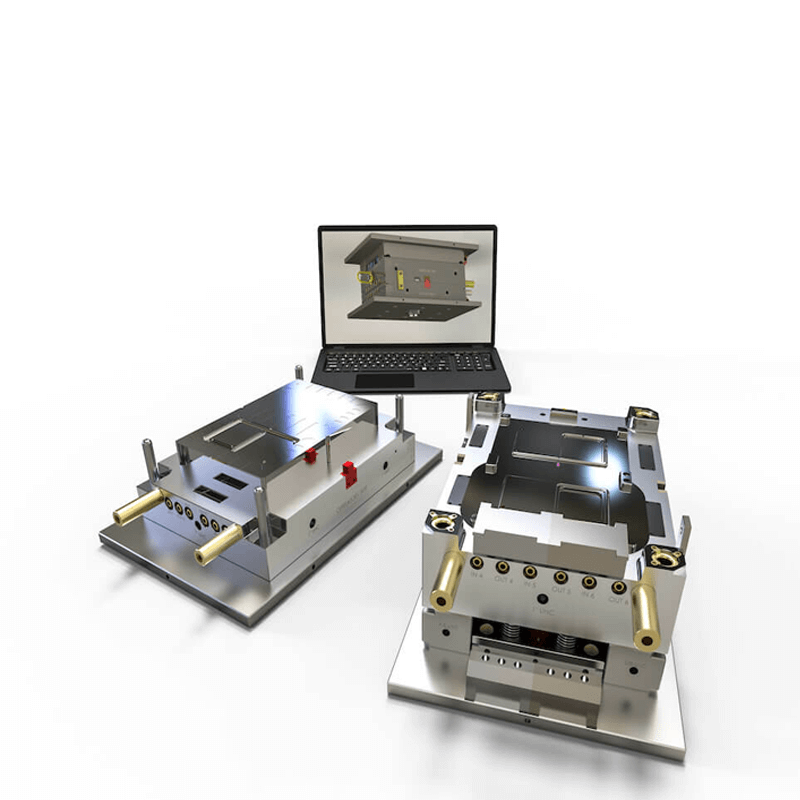
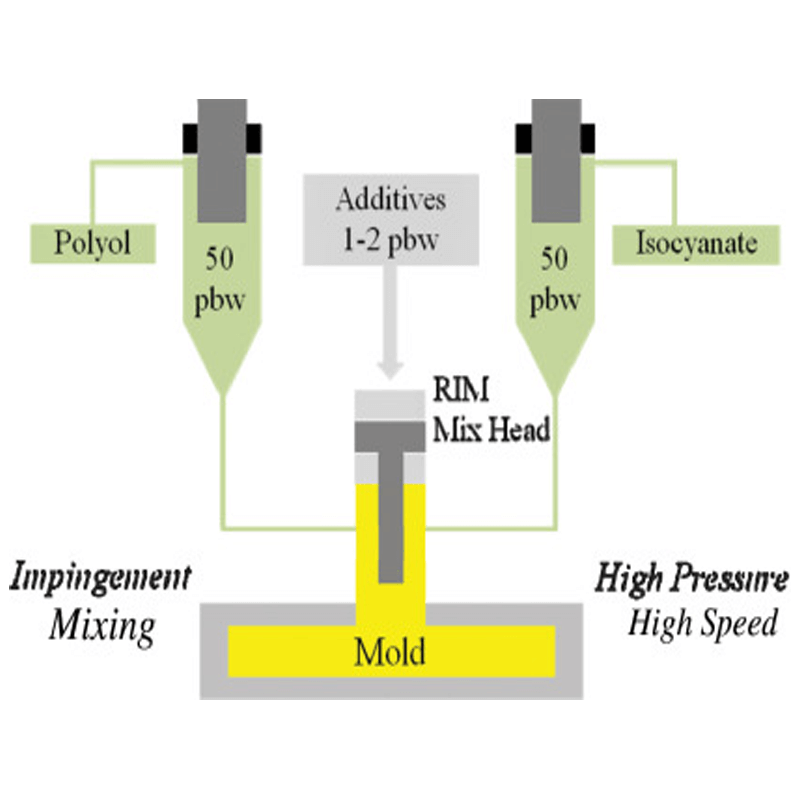
Efficient Short-Run Production with Advanced Mold Making
Our Reaction Injection Molding (RIM) process is designed to offer cost-effective solutions for short-run production of molded plastic parts. We specialize in delivering small production batches with just-in-time (JIT) shipping, reducing your inventory costs and enhancing your flexibility to make design adjustments.
We utilize high-quality, economical aluminum tooling in our mold making process, ensuring that even small batches of parts are produced with exceptional quality and tight tolerances. This approach supports thousands of cycles while maintaining consistency across every part.
RIM technology is particularly advantageous for complex designs, allowing for more intricate geometries and highly stylized features that were previously challenging to achieve. By integrating advanced mold making with our RIM capabilities, we provide a robust solution for precise, high-quality production tailored to your specific needs.
Comprehensive Assembly Solutions for Tooling
We offer a full spectrum of assembly services that complement our precision tooling capabilities. Our value-added services include sourcing, procurement, sub-assembly, and complete assembly of component parts.
We efficiently source and procure a diverse range of components, from metals and plastic parts to standard hardware and custom elements. Our expertise extends to integrating all types of mechanical and electro-mechanical components into sub-assemblies, ensuring seamless integration with our high-quality tooling. By combining meticulous assembly processes with our advanced tooling solutions, we deliver fully assembled, ready-to-use components that meet the highest standards of quality and precision.
Surface Options for Tooling Making
When it comes to tooling making, selecting the right surface treatment is crucial for achieving optimal performance and longevity. Here are six common surface options used in the industry:
1. Hard Anodizing: This electrochemical process enhances the surface hardness and corrosion resistance of aluminum molds. It provides a durable, wear-resistant coating that extends the tool’s lifespan and improves its overall performance.
2. Polishing: A mechanical process that smooths the mold surface to a high shine. Polishing reduces friction and improves the aesthetic finish of the molded parts, making it ideal for applications where appearance and smoothness are critical.
3. Nickel Plating: Applied as a protective layer to prevent corrosion and wear. Nickel plating also improves the tool's hardness and is often used for molds that require additional durability and resistance to chemicals.
4. Chromium Plating: This process deposits a thin layer of chromium onto the tool surface, offering exceptional hardness and resistance to abrasion. It is particularly effective for reducing friction and enhancing the mold's performance in high-wear applications.
5. Electroless Plating: A chemical process that deposits a uniform layer of metal onto the mold surface without the need for electric current. This treatment provides excellent corrosion resistance and wear protection, suitable for a variety of mold materials.
6. Ceramic Coating: This high-performance coating enhances the mold’s resistance to high temperatures, chemicals, and wear. Ceramic coatings are ideal for molds exposed to harsh conditions or requiring superior durability and longevity.
Each of these surface options is tailored to meet specific requirements and conditions, ensuring that tooling maintains its performance and extends its service life.