About Our Overmolding & Insert Molding
The insert molding process entails injecting molten plastic around strategically positioned inserts, typically made of metal. This method establishes a robust bond between the plastic and the insert, effectively reducing the need for additional assembly operations and saving valuable time. Common types of inserts used in this process include pins, blades, threaded nuts and knobs, sleeves, bushings, and metal shanks, such as those found in tools like screwdrivers. This technique ensures a durable, integrated component, enhancing both efficiency and product reliability.
Overmolding allows manufacturers to produce components from multiple materials through either a manual two-stage process for small production runs or an automated two-stage process for larger-scale operations. Regardless of the production volume, the overmolding process follows a specific sequence. Initially, a thermoplastic injection forms the rigid substrate. Once the substrate is set, a secondary injection—typically a thinner, more flexible material—is applied in, on, or around the substrate. As the materials cool, they bond together, forming a cohesive, robust, and durable part. The bond between the materials can be either chemical or mechanical, depending on the material properties and the specific design of the component or product.
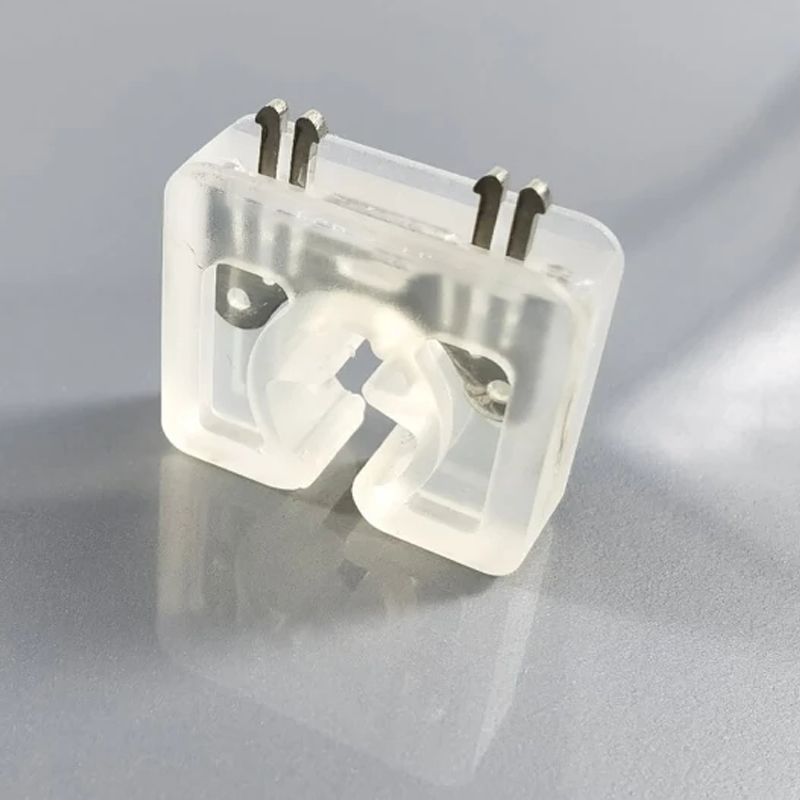
Why Choose Us For Your Overmolding & Insert Molding Parts?
Our expertise lies in delivering high-performance LSR silicone products through cutting-edge injection molding techniques. Injection molding is a precise manufacturing process where molten material is injected into a meticulously designed mold. Under controlled high temperatures and pressures, the material is shaped and solidified before being cooled and ejected. By employing high-precision molds, we can efficiently produce thousands of identical, high-quality components, ensuring consistency and reliability.
Protection & Durability
Overmolding is a sophisticated technique that integrates elastomeric materials such as silicone with other substrates to meet the diverse demands of various applications. This method enhances the performance and durability of silicone products across multiple industries:
- Soft Touch: Provides a comfortable, tactile surface that improves grip and user experience.
- Anti-Slip: Ensures secure handling by reducing slippage, ideal for tools and consumer products.
- Waterproofing: Creates effective seals and gaskets, crucial for protecting electronics and automotive components from moisture and contaminants.
- Insulation: Offers superior electrical insulation properties, essential for components that require isolation.
Design Flexibility
The overmolding process affords significant design flexibility, allowing for the customization of silicone products to meet specific performance criteria. Whether the goal is to enhance strength, durability, waterproofing, sealing, corrosion resistance, or electrical conductivity, overmolding enables the creation of tailored solutions for a wide array of applications. This adaptability is particularly valuable in industries where precise specifications and high performance are critical.
Enhanced Functionality
The functionality of silicone products can be significantly improved by integrating additional components, such as electronic connectors, threaded inserts, or bearings, into the overmolded parts. This process not only enhances the strength and load-bearing capacity of the final product but also makes it suitable for more demanding applications. The ability to combine multiple materials and components in a single manufacturing step streamlines production while enhancing the product's overall performance.
Aesthetic and Branding Advantages
Beyond functionality and protection, overmolding also offers aesthetic and branding benefits. Silicone products can be produced in a variety of colors, textures, and finishes, allowing for visual appeal and brand differentiation. This is particularly important in consumer-facing industries where the appearance of a product can impact consumer choice. Moreover, logos and other branding elements can be directly integrated into the product design, ensuring a cohesive and professional appearance.
By leveraging these advanced techniques, we deliver silicone products that are not only high-performing but also precisely tailored to meet the unique needs of our clients across various industries.
Comparison: Insert Molding, Overmolding, and Injection Molding
Both insert molding and overmolding are advanced techniques within the broader category of injection molding, designed to integrate distinct parts into a cohesive component.
Insert Molding involves embedding a preformed insert, such as a threaded rod or bushing, into molten silicone resin within a mold. This process creates a singular part where the silicone encapsulates the inserted material, achieving seamless integration in a single step. This method is particularly advantageous for silicone products, as it enhances the functionality and durability of the final component by combining different materials into one robust piece.
Overmolding also integrates multiple parts but does so in a two-step process. It involves applying a layer of silicone over an existing part, typically made from a different material, to create a unified component. For example, in manufacturing silicone products, overmolding might be used to add a soft, ergonomic grip to a rigid plastic base, resulting in a single product that combines the properties of both materials.
While both processes aim to produce a unified component, they differ in execution. Insert molding encapsulates a smaller part within silicone, merging it directly with the resin during the injection process. In contrast, overmolding involves first molding the base component and then adding a secondary silicone layer, creating a multi-material product.
For silicone products, these techniques offer distinct advantages. Insert molding is ideal for applications requiring embedded components with high precision and durability, while overmolding is better suited for enhancing the tactile properties and aesthetics of silicone products, such as adding soft-touch grips or insulating layers.